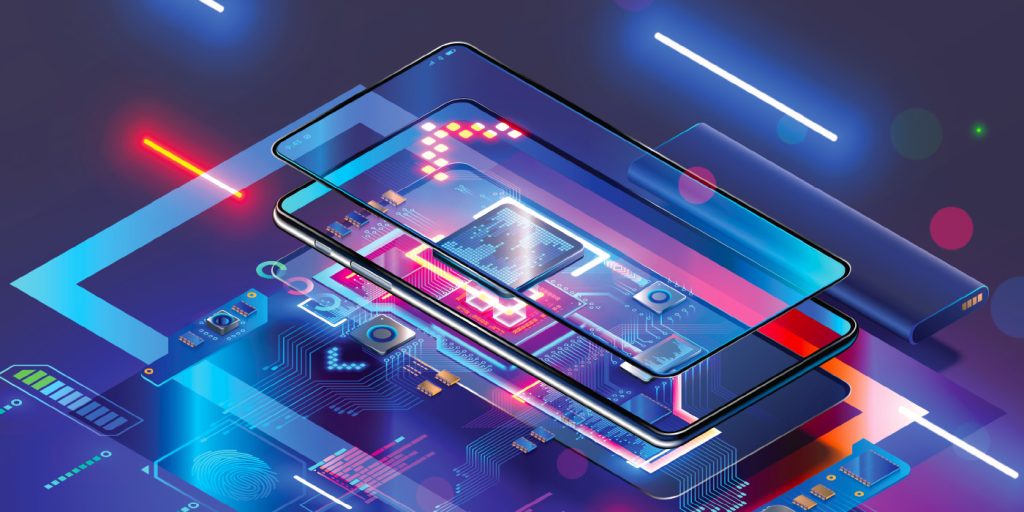
Glass is a hugely versatile material. Tempered glass, for example, can be produced simply by changing the heating and cooling process during manufacturing. Changes to the shape of glass lenses alter their optical characteristics, while the introduction of pores into bulk glass enables a range of high-tech applications like bio-scaffolds and catalyst supports. Modifications to the chemical composition of glass – for example, through the use of glass modifiers – can change almost all of its properties, enabling the production of corrosion-resistant labware and high-resistance electrical components.
Depositing films on glass provides a way of augmenting the properties of glass without changing the glass itself. From thin-film solar cells to heating elements integrated directly onto glass surfaces, these films enable products and components which combine the properties of glass with those of other materials and technologies.
Film deposition can largely be divided into two categories: thin film deposition and thick film deposition. As we mention in our article on glass films, there is some overlap between the actual thickness of films in these categories – however, “thin films” and “thick films” remain distinct primarily due to differences in the technology used to produce them. Thin films typically range from less than a nanometer to several microns in thickness and are typically produced by sophisticated processes such as vapor deposition. Thick films, on the other hand, generally range from several microns up to a millimeter in thickness; and are usually deposited in the form of inks or pastes via processes like screen printing or tape-casting.
Depositing Thick Films on Glass
Electronics
Thick films are widely used in electronics: alternating layers of conductive and resistive materials can be deposited and patterned onto a substrate to build up electric circuits. While ceramic substrates are common, it is not unusual for these films to be deposited onto glass instead.
In these applications, thick films are typically deposited on glass via screen printing, forming layers between 5 and 20 μm in thickness. Insulating thick film pastes will often contain glass in the form of frit to provide high resistivities.7 After deposition, these thick films are typically fused at high temperatures before the next layer is deposited, providing a reliable and low-cost route to the fabrication of microelectronic devices.
One alternative application of thick is the production of printed heater elements on glass substrates.8 Directly depositing a heating element onto glass enables the construction of self-defrosting windows or glass appliances (such as kettles and cookers) which provide uniform heating with the modern appearance of glass.
Thick films offer the advantage of versatile and low-cost fabrication, making them ideal for the production of electronic components throughout a wide range of industries. For precision applications, however, thin film technologies provide much greater control over film thickness and surface characteristics.
Depositing Thin Films on Glass
Optics
One of the primary application areas of thin films on glass is in optics: in fact, the most famous application of thin films is probably the household mirror, which is produced by depositing a thin metal layer on the back of a sheet of glass to increase its reflectivity.
Depositing thin films on glass can produce optical interference effects, which result in certain regions of wavelengths being transmitted, reflected, or absorbed.2 Such films modify light by virtue of their nanoscale structure rather than the color of the bulk material itself, enabling optical parameters such as reflectivity and the color of transmitted light to be precisely tuned by changing layer thickness. The wings of some species of butterfly use the same fundamental “optical thin film” principles to produce their striking iridescent coloring.3
Low emissivity (or “Low-e”) glass is a major application of thin film deposition on glass. Produced through successive deposition of thin metal oxide films on glass, it allows the transmission of visible light while reflecting radiated heat (i.e., the infrared portion of the spectrum). Such optical films enable Low-e windows to reflect the sun’s light in hot environments or to prevent heat loss through windows in cold environments.
Similarly, these films enable anti-reflective coatings, which reduce glare in architectural applications as well as in consumer electronics.
High-precision deposition of thin optical films enables the construction of specialist optical filters such as dichroic filters. These filters rely on extremely precise film deposition to transmit or reject specific wavelength bands for precision applications in research and industry.
Electronics
Glass substrates for thin films have a number of special roles in electronics — particularly in the fabrication of transparent conducting films (TCFs). TCFs are a special type of film made of materials that are optically transparent and electrically conductive. They are fabricated by depositing or growing thin films of materials such as metal oxides — or even graphene — on glass substrates (with the glass offering the additional benefit of blocking infrared wavelengths of light). TCFs are applied in a range of devices, including LCD and OLED displays, touchscreens, and photovoltaic panels.4
Depositing conductive traces directly onto glass substrates enables circuitry and functional electronic components to be integrated into glass, with widespread application in aviation, automobiles, and consumer electronic devices such as smartphones.5 Other applications of thin films on glass substrates in electronics include the manufacture of thin film resistors and transparent electrodes produced by sputtering metal films onto glass.6
At Mo-Sci, we are experts in creating custom glass solutions for unique and demanding applications: whether that is glass substrates for a specific thin film application or ultra-pure glass frit for the production of resistive thick film pastes. To find out more about our services and capabilities, get in touch with us today.
References and Further Reading
- Bach, H. & Krause, D. Thin Films on Glass. (Springer Science & Business Media, 2003).
- Anderson, A.-L., Chen, S., Romero, L., Top, I. & Binions, R. Thin Films for Advanced Glazing Applications. Buildings 6, 37 (2016).
- Butterflies Hack Light Waves to Produce Brilliant Color — Biological Strategy — AskNature. https://asknature.org/strategy/wing-scales-cause-light-to-diffract-and-interfere/.
- Rosli, N. N., Ibrahim, M. A., Ahmad Ludin, N., Mat Teridi, M. A. & Sopian, K. A review of graphene based transparent conducting films for use in solar photovoltaic applications. Renewable and Sustainable Energy Reviews 99, 83–99 (2019).
- Kim, H.-G. & Park, M.-S. Fast Fabrication of Conductive Copper Structure on Glass Material Using Laser-Induced Chemical Liquid Phase Deposition. Applied Sciences 11, 8695 (2021).
- Thin Film Applications | Bourns. https://www.bourns.com/pdfs/thinfilm.pdf.
- Zargar, R. A. & Arora, M. Screen Printed Thick Films on Glass Substrate for Optoelectronic Applications. in Photoenergy and Thin Film Materials (ed. Yang, X.) 253–282 (Wiley, 2019). doi:10.1002/9781119580546.ch6.
- Radosavljevic, G. & Smetana, W. 15 – Printed heater elements. in Printed Films (eds. Prudenziati, M. & Hormadaly, J.) 429–468 (Woodhead Publishing, 2012). doi:10.1533/9780857096210.2.429.