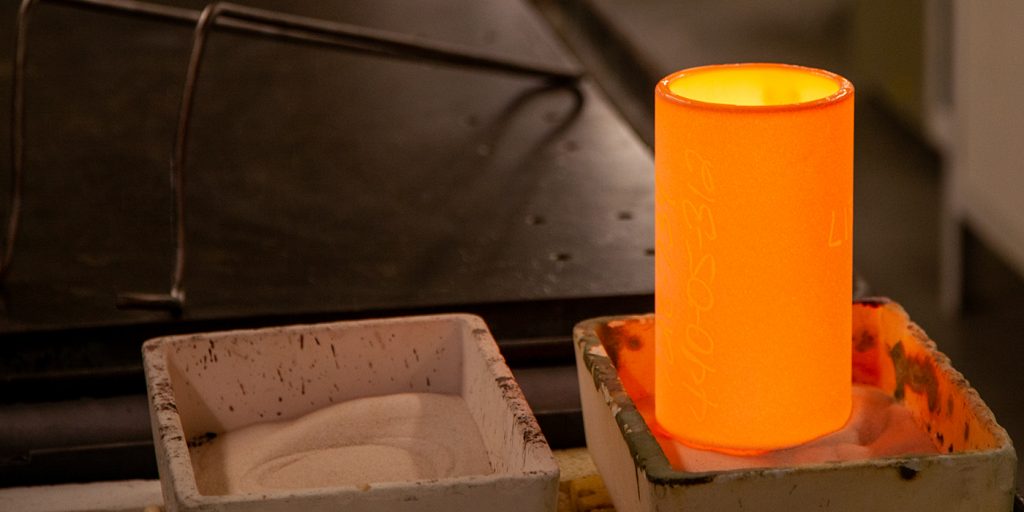
When developing a new glass melt, it is critical that the right crucible is chosen to ensure that the crucible doesn’t crack, deform or contaminate the melt. Often crucibles are used repeatedly and need a long working lifespan, as any downtime caused by a crucible being out of action is likely to stop large parts of the manufacturing process, which can be incredibly costly.
The crucible’s composition should be evaluated for factors including maximum operating temperature, resistance to thermal shock, expansion coefficient, compressive strength and potential reactions with the glass,1 balanced with the longevity and cost of the material.
Silica
Silica (SiO2) is an oxide that can operate at high temperatures without loss of structural integrity and chemical composition. The maximum operating temperature of 1500 °C is lower than other materials, including alumina. But with a higher resistance to thermal shock and an extremely low coefficient of thermal expansion, silica is an excellent choice for melting many glass families such as soda-lime, silicates, and borosilicates.
Alumina
For melts where high temperature stability is required, but cost is also a factor, alumina (Al2O3) is a viable candidate. Alumina has a high thermal conductivity making it more efficient at transferring heat from the furnace. It also has a low coefficient of thermal expansion, which leads to good thermal shock resistance. The maximum operating temperature is 1,700 °C for high purity Al2O3.
Another attractive feature is its resistance to chemical attack that can cause serious degradation of the crucible and contamination of the melt. In the case of heavy metal oxide (HMO) glass melting its resistance is better than even that of platinum.2
AZS (alumina-zirconia-silica)
AZS is one of the mostly widely used refractories in commercial glass production, and can withstand high temperatures as well as being highly resistant to corrosion.3 The oxides that make up AZS are inexpensive, and the resulting mixture can be cast into many different crucible shapes.
The main drawback, is that when a glass melt comes into contact with the walls of the AZS crucible, flaws such as bubbles and knots can be formed, resulting in a compromised structure. This is a serious problem, especially in industrial glass production where it is estimated that up to 10% of the glass produced in continuously operating furnaces is rejected. One solution that is being explored is the development of ultra-low exudation AZS.4
Platinum
One of the noble metals, platinum is highly inert making it one of the first choices for researchers looking to avoid contamination in their samples.5 However, its scarcity and difficulty in mining makes it an expensive option for crucibles.
To lower the cost without compromising on operation, platinum is often alloyed with rhodium in ratios of 80:20 or 90:10. This can actually increase the operating temperature to around 1,600 °C; 300 °C higher than that of pure platinum.6 Platinum is also a relatively malleable metal which allows it to be easily formed into crucibles of all different shapes and sizes.
Although resistant to most forms of corrosion, platinum crucibles can be attacked by heavy metal oxide glasses, causing degradation of properties in the final material.
Vitreous Carbon
Vitreous carbon is a ceramic material produced by the thermal decomposition of a cross-linked polymer.7 It is also known as “glassy” carbon due to its black color and high sheen. Similar to glass it is quite fragile, but it has other key features that make it well suited as a crucible material.
Along with a high operating temperature of up to 2,500 °C, it is resistant to thermal shock and as it is made of carbon has a relatively good thermal conductivity. A key feature is that it has exceptionally low porosity and is impervious to gas, as well as highly resistant to attack by numerous chemicals including hydrochloric, hydrofluoric, nitric, sulfuric and chromic acids. It is more expensive than other ceramic crucibles such as alumina, but with a better lifetime due to its stability during thermal cycling.
Fire Clay
A material that has been used throughout history for glass melt crucibles, clay is abundantly available and easily formed into a wide variety of shapes. Modern fireclays can also be tailored to specific applications by altering the composition with oxides and other additives.8 By adding common compounds such as K2O, Na2O, CaO and MgO, the maximum operating temperature can be raised significantly.
Some fire clays can be high in silicon oxide (SiO2) which lowers the thermal shock resistance, and some may possess a high porosity. Pores can allow the glass melt to penetrate the crucible, raising the risk of contamination and even leading to breakage of the crucible itself.
References
- J.E., S. Introduction to Glass Science and Technology. doi:10.1017/CBO9781107415324.004
- Dos Santos, I. M. G. et al. Ceramic crucibles: A new alternative for melting of PbO-BiO 1.5 -GaO 1.5 glasses. J. Non. Cryst. Solids 319, 304–310 (2003).
- Magnificus, D. R. Glass Defects Originating from Glass MelUFused Cast AZS Refractory Interaction. (1994). doi:10.6100/IR417346
- Cabodi, I., Gaubil, M., Morand, C. & Escaravage, B. ER 2001 SLX: Very low exudation AZS product for glass furnace superstructures. Glas. Technol. Eur. J. Glas. Sci. Technol. Part A 49, 221–224 (2008).
- Fischer, B. & Gerth, K. Platinum for Glass Making at Jena. Platin. Met. Rev. 38, 74–82 (1994).
- Improving Service Life of Platinum Crucibles Used for Sample Fusion. AZoNetwork Available at: https://www.azom.com/article.aspx?ArticleID=17601.
- Cowlard, F. C. & Lewis, J. C. Vitreous carbon – A new form of carbon. J. Mater. Sci. 2, 507–512 (1967).
- ‘Crucible’ from DigitalFire.com Reference Library. Available at: https://digitalfire.com/4sight/glossary/glossary_crucible.html.