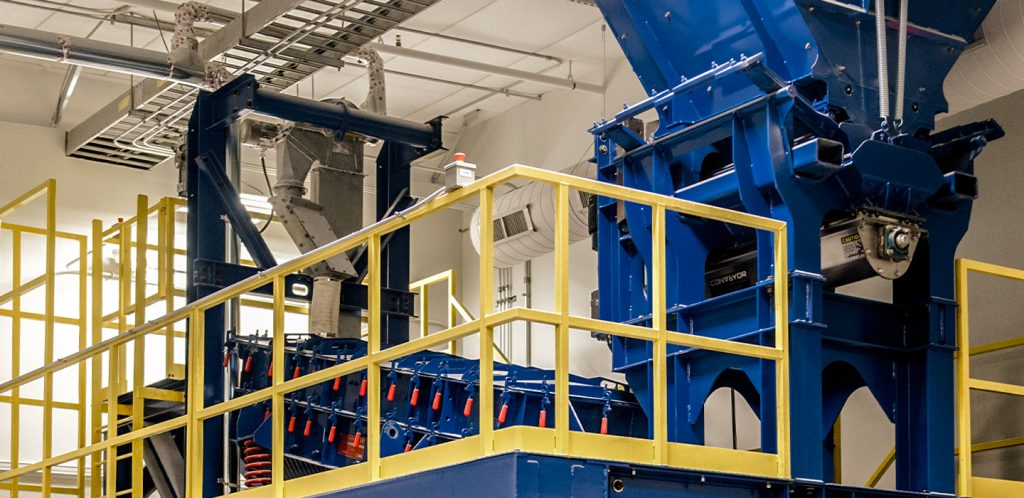
Milling is an effective top-down process for producing glass powders with particle sizes ranging from nanoscale to micron-size. This article provides a guide to the various types of milling processes used by Mo-Sci to produce our range of specialty glass powders.
Alongside microspheres and ingots, one of the primary forms in which Mo-Sci provides glass is as a powder. Powdered glass has numerous applications throughout research and industry. For example, glass nanofillers offer unique advantages in developing composite materials for medical and dental prosthetics.1,2 Such composites are not only incredibly strong, but exhibit superior biocompatibility due to their surface roughness, hydrophobicity, and chemical inertness.
While glass powders and nanofillers can be produced via “bottom-up” methods such as the sol-gel process, such techniques are not always practical, especially when producing glass particles with complex compositions.3 In these situations, a “top-down” solution is preferred: larger particles of glass can simply be broken down into smaller particles in a process known as milling.
Note that in the world of machining, “milling” has two meanings: it can refer either to grinding (e.g., using a ball mill) or cutting (e.g., using a CNC mill). Here, we’re strictly using the term in the former sense.
Glass Milling Processes
Jaw Crusher
A jaw crusher produces the coarsest grind out of any of the processes in this list. Much like a nutcracker, a jaw crusher uses direct application of compressive force between two mechanical “jaws” to fracture solid materials. The jaws are typically arranged vertically so that the gap between them narrows as material falls through the system. The particle size decreases as the material moves down through the crusher. Crushed material escapes through the narrow gap at the bottom between the jaws after it has been processed. Jaw crushers are heavy-duty machines often used for mining and quarry applications, and are suitable for continuous use with materials across a wide range of hardness. Jaw crushers are typically used to process larger fragments of material and are not capable of fine grinding. They may be used as a preliminary step before more controlled grinding in a ball mill or jet mill.
Hammer Mill
With more precision than a jaw crusher, a hammer mill (or hammer crusher) can crush aggregate material into smaller particles using hammers. Commonly used for processing papers, organic waste, and foodstuffs such as grain and fruit; hammer mills can also be used to produce glass powder. Available in configurations with one or several rows of hammers, hammer mills are high-durability devices capable of coarse grinding.
Ball Mill
Ball milling is one of the most commonly used techniques for milling glass, thanks to its adaptability and relatively low cost. A ball mill for glass processing consists of a rotating or vibrating ceramic-lined drum, inside which are a number of balls that act as the grinding medium. These can be made from a variety of hard and durable materials such as alumina or zirconia. Glass is added to the drum, and the continuous impact and attrition between the balls and the glass as the drum rotates breaks the glass down into small particles.
Ball mills are supremely versatile, they exist in a wide range of sizes, can perform wet or dry milling, and can accommodate a wide range of different grinding media. Ball mills are suitable for either batch or continuous processing, and grind size can be controlled by changing the diameter size of the balls. Industrial ball mills may be used to coarsely crush relatively large pieces of material, whereas lab-grade ball mills are capable of finely milling glass to micron level and below. So-called “high energy” ball milling can even be used to reliably grind the material into nanoscale particles.4
Centrifugal Mill
Most centrifugal mills lie firmly in the realm of labware. Inside a centrifugal mill, shearing action between a rotor and a fixed sleeve breaks material down in a relatively well-defined manner. High rotational speeds (up to several tens of thousands of RPM) enable fast and finely controlled grinding of small batches of material, often using sieves to enable the extraction of particles with sizes in the tens of microns region.
Jet Mill
Another precision piece of equipment, a jet mill uses a high-velocity flow of gas or compressed air to cause glass particles to collide with each other inside a chamber. A process known as cyclonic separation enables particles to leave the gas stream once they have reached a sufficiently small size. Consequently, jet mills can continue milling particles of glass until they reach the desired size, resulting in a glass powder with very little variation in particle size.5 Like ball mills, jet mills are capable of grinding glass powder down to sub-micron particle sizes.
Milled Glass Powders from Mo-Sci
At Mo-Sci, we are experienced in the use of all of these milling methods to produce a wide variety of specialty glass powders, including those made from complex formulations which are difficult to find elsewhere. As well as using different types of mills, we make use of various milling media (such as alumina, zirconia and yttria-stabilized zirconia (YSZ)), and perform wet milling in water or alcohol to achieve superior results.
To find out more about our capabilities in the specialty glass powders market, get in touch with the Mo-Sci team today.
References and Further Reading
- Velez, M. et al. Processing of yttrium aluminosilicate (YAS) glasses for dental composites. Cerâmica 57, 1–9 (2011).
- Erol-Taygun, M., Zheng, K. & Boccaccini, A. R. Nanoscale Bioactive Glasses in Medical Applications. Int J Appl Glass Sci 4, 136–148 (2013).
- Vital, A. et al. Ultrafine comminution of dental glass in a stirred media mill. Chemical Engineering Science 63, 484–494 (2008).
- Yang, L. 2 – Nanotechnology-enhanced metals and alloys for orthopedic implants. in Nanotechnology-Enhanced Orthopedic Materials (ed. Yang, L.) 27–47 (Woodhead Publishing, 2015). doi:10.1016/B978-0-85709-844-3.00002-1.
- Wachtman, J. B. Materials and Equipment – Whitewares Manufacturing. (John Wiley & Sons, 2009).