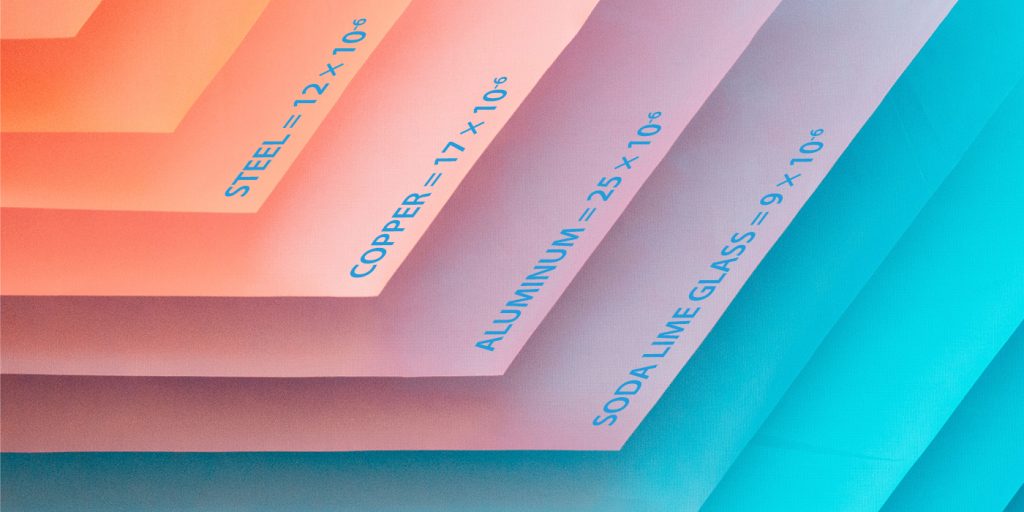
The coefficient of thermal expansion (CTE) is a critical parameter to consider in product design. Defined as how the length and/or volume of a material changes in response to temperature change, components under varying conditions must move and expand together to prevent structural damage or gaps that cause seals to fail.
Sealing glass is a frequently used material, especially in high-temperature environments, as the glass characteristics (including the CTE) can be manipulated to match the required specifications. Sealing glasses are commonly used in lighting headers, high-temperature sensors, thermocouples and heater components, solar cells, molten sodium batteries, solid oxide fuel cells and many others where a glass-metal or glass-ceramic seals are required.1
Sealing Glass in Solid Oxide Fuel Cells
Solid oxide fuel cells (SOFCs) offer a low-pollution electrochemical method of generating electricity with high efficiencies.2 SOFCs produce less sulfur and nitrogen oxide emissions, contain fewer moving parts and are generally more efficient than combustion engines and generators.
Many automobile manufacturers, including Toyota, Hyundai, and Honda are investigating hydrogen fuel cell options to produce hydrogen-powered cars. SOFCs are ideal for cars as they are quiet and free from vibration.
SOFCs use a fuel (e.g. hydrogen) and an oxidant (e.g. O2 gas) that are separated by a hermetically sealed barrier, which stops the gas escaping, as well as being electrically insulating.3
Glass is the most commonly used material for these seals because it is low cost, relatively easy to produce, and its properties, including the CTE and glass transition temperature, can be tailored to meet specific operating requirements.
These glass seals for the hermetic chambers are manufactured by applying the glass as a slurry or preform to the substrate of interest and heat treating it, allowing the glass to crystallize in a controlled way to form the seal.
It is incredibly important that the glass has sufficient strength, as glass-ceramic seals are vulnerable to fracture due to thermal stress. If the seal were to fail then the component would lose functionality and would need to be replaced.
The sealing glass must also be chemically compatible with all other fuel cell materials and be able to work at high temperatures over an operating lifespan of at least 40,000 hours.
However the critical factor for SOFC sealing glass is that the CTE is matched between the glass and other components, so that they can respond appropriately as the temperature of the cell increases or decreases. Typical operating temperatures are around 550-800 °C, but they can be much higher for high temperature variants.
Meeting CTE Challenges with Viscous Glass Seals
Mo-Sci manufactures many different CTE-matched glass-metal and glass-ceramic seals with good strength, which can also withstand temperatures up to 1,600 °C.
We have been building on this experience to create a new type of sealing glass, where the seals do not crystallize and remain viscous during operation. This still allows the glass to bond to metals and ceramics, but the join is much more resistant to thermal stresses.
These sealing glasses have been designed to be non-crystallizing and have a glass transition temperature (Tg) below that of the normal operating temperature of the SOFC.4 The viscous nature of the seal makes it inherently more resistant to thermal stresses than a rigid seal, as they are relieved at temperatures above Tg, lowering the range of temperatures at which thermal stresses develop.
Another benefit of viscous glass seals is that any flaws within the seal, or at the interface, will ‘heal’ as they are heated. This is due to the viscous state of the glass at higher temperatures, allowing it to flow into breakages and repair the cracks. In one test, a composition of alkali-free barium borosilicate glass self-healed deliberate cracks after the seal was reheated in air for just two hours at temperatures as low as 744 °C.5
For more information on sealing glass technology from Mo-Sci, visit our Sealing Glass page or contact us.
References
- Donald, I. W., Mallinson, P. M., Metcalfe, B. L., Gerrard, L. A. & Fernie, J. A. Recent developments in the preparation, characterization and applications of glass- and glass-ceramic-to-metal seals and coatings. J. Mater. Sci. 46, 1975–2000 (2011).
- Singhal, S. C. Solid oxide fuel cells for stationary, mobile, and military applications. Solid State Ionics 152–153, 405–410 (2002).
- Fuel, O. & Ill, C. Advances in Solid Oxide Fuel Cells IV. (2008).
- Hsu, J. H., Kim, C. W. & Brow, R. K. Interfacial interactions between an alkali-free borosilicate viscous sealing glass and aluminized ferritic stainless steel. J. Power Sources 250, 236–241 (2014).
- Hsu, J. H. et al. An alkali-free barium borosilicate viscous sealing glass for solid oxide fuel cells. J. Power Sources 270, 14–20 (2014).