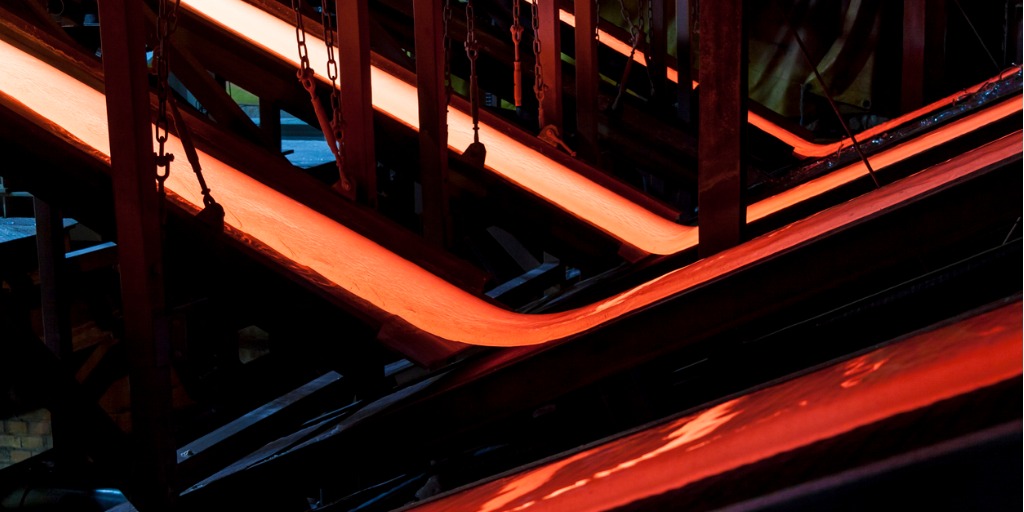
Humans have been making glass for over three thousand years.1 Despite its age, glass is both ubiquitous and cutting-edge, having found tried-and-tested applications in architecture, transportation, and insulation; as well as more novel applications in electronics, biomaterials, and renewable energy.2,3
Much has changed in three thousand years, and as we continue to designate glass to new applications, the technology that we use to produce various types of glass has improved and diversified. At Mo-Sci, for example, we use a variety of glass production methods to produce glasses with varying hardness, thermal shock resistance, electrical conductivity, optical characteristics, and many other properties. In this article we examine some of the most common glass production methods and furnace types and how they’re used to produce glass for different applications.4
Types of glass production processes
Almost all glass is produced in a furnace, where a precise mixture of raw materials is combined and melted into a homogeneous mixture. Like many industrial manufacturing processes, glass melting can be broadly categorized as either a continuous or discontinuous (batch) process.
Continuous glass production
Continuous glass melting processes work like a production line: a mixture of raw ingredients is added continuously at one end of the furnace, and glass is extracted continuously at the other. Continuous melting processes are high-throughput and preferred wherever a high volume (say 100-500 tons per day) of the same type of glass is required. Continuous processing is typically used for production of architectural glass, fiberglass, screens for consumer electronics, and food and beverage containers.
Discontinuous or batch production
In discontinuous or batch processing, a batch of raw materials is added to a single melting vessel and melted into glass. Once the glass is formed, it can be removed from the vessel and formed into products. Batch-processing glass in this manner trades throughput for flexibility, enabling manufacturers to produce multiple formulations of glass depending on customer demand, without cross-contamination.
Discontinuous glass melting is typically used for smaller production runs and is often required for uncommon glass types with relatively niche applications such as optics, electronics or signal applications.
Types of glass furnaces
The melting point of most glasses lies around 1,400-1,600°C, depending on its composition. As a result, glass production requires a great deal of heat energy, usually provided in the form of natural gas injected into a combustion chamber. Because of this high energy demand, glass furnaces are constructed to minimize heat loss, and often feature some form of waste-heat reclamation system.
Regenerative glass furnaces
Regenerative furnaces are one such example: these furnaces pipe hot exhaust gas out via a regeneration chamber containing a ‘checkerwork’ of refractory bricks – often referred to simply as ‘checkers’. These bricks have a high resistance to thermal shock as well as high specific heat capacity, and act as a thermal energy store.
Regenerative furnaces run in cycles: the direction of gas flow is periodically reversed so that combustion gas is passed over the now-hot refractory bricks on the way to the combustion chamber, absorbing and making use of the waste thermal heat from the previous half-cycle.
Regenerative furnaces always have an even number of regeneration chambers, so that heat regeneration can occur in both directions. Regenerative glass furnaces can be either cross-fired or end-fired depending on application: cross-firing, the use of multiple combustion gas inlets down opposing sides of the furnace, allows more precise control over the location and temperature of hot spots within the furnace; while end-firing (a single inlet of combustion gas at the end of the chamber) generally reduces structural heat losses due to the increased residence time of the combustion gases.5
Recuperative glass furnaces
Recuperative furnaces employ a slightly different approach to reclaim waste heat. In this type of furnace, the chimney and gas inlets are coupled with a radiative heat exchanger.
This enables the continuous transfer of heat from exhaust gas to combustion gas, without the requirement for gas flow reversal as in regenerative furnaces. This enables recuperative furnaces to be employed for continuous glass melting applications, while also offering a relatively low investment cost.
The absence of regeneration chambers also simplifies construction of the furnace and results in a smaller footprint; however, the heat transfer efficiency of recuperative furnaces is generally lower than that of regenerative furnaces.6
Oxygen-fuelled (“oxy-fuel”) glass furnaces
Oxygen-fuelled (“Oxy-fuel”) glass furnaces are a relatively new way of tackling the problem of high heat energy demand: by replacing the air entering the furnace with oxygen (typically at over 90% purity), the total amount of gas entering the chamber can be reduced while maintaining the same combustion energy input.
This means the energy required to heat the input gas is reduced, while also reducing waste heat in exhaust gas. Other furnaces waste a large amount of energy simply heating the nitrogen in the air.
In general, oxy-fuel furnaces have the same basic design as recuperative furnaces, with multiple lateral burners and a limited number of exhaust ports. Most oxygen-fired glass furnaces don’t use heat recovery systems to pre-heat the oxygen supply to the burners, although there are some developments in oxygen and natural gas preheating.
The benefits of oxy-fuel furnaces include cheaper furnace designs, lower NOx emissions per ton of molten glass, smaller flue gas volumes, smaller footprints for furnace systems, and reductions in fuel consumption.7
While oxygen costs may potentially exceed the reduction in fuel costs, research indicates that switching to an oxy-fuel furnace substantially reduces energy costs for both large and small glass manufacturing operations.8
All-electric glass furnaces
Electrically heated furnace technology is nearly as old as regenerative furnace technology.9 These work in a radically different way to conventional furnaces, avoiding combustion altogether and instead imparting heat energy to the glass mixture using high-voltage electrodes. These are typically used for fiberglass production but are also used for specialty glasses.
Typically used for small-batch production, all-electric furnaces offer high thermal efficiency, a high degree of control over temperature, and can yield highly homogeneous glass while minimizing atmospheric pollution and economizing raw materials that volatilize readily.10
References
- Glass Timeline – Important Dates and Facts. Available at: http://www.historyofglass.com/glass-history/glass-timeline/. (Accessed: 22nd January 2019)
- Bioactive Glass – Mo-Sci Corporation. Available at: https://mo-sci.com/bioactive-glass. (Accessed: 22nd January 2019)
- Glass – Mo-Sci Corporation. Available at: https://mo-sci.com/sealing-glass. (Accessed: 22nd January 2019)
- Lecture 3: Basics of industrial glass melting furnaces IMI-NFG Course on Processing in Glass. Hubert, M. (2015).
- Regenerative Furnaces | Industrial Efficiency Technology Database Available at: http://ietd.iipnetwork.org/content/regenerative-furnaces. (Accessed: 22nd January 2019)
- Recuperative Furnaces | Industrial Efficiency Technology Database
Available at: http://ietd.iipnetwork.org/content/recuperative-furnaces. (Accessed: 17th June 2019) - Oxy-Fuel Furnace | Messer Group
Available at: https://www.messergroup.com/minerals/glass/oxyfuel-furnace. (Accessed 17 June 2019) - Energy Efficiency Improvement and Cost Saving Opportunities for the Glass Industry An ENERGY STAR® Guide for Energy and Plant Managers. Worrell, E., Galitsky, C., Masanet, E. & Graus, W. (2008).
- “The Efficient Future for the Glass Industry Is ‘All-Electric.’” Eurotherm by Schneider Electric, 27 Dec. 2018, https://www.eurotherm.com/en/glass-news/the-efficient-future-for-the-glass-industry-is-all-electric/.
- Electric melting of glass. Stanek, J. & Matej, J. J. Non. Cryst. Solids 84, 353–362 (1986).
- Glass Products – Mo-Sci Corporation. Available at: https://mo-sci.com/en/products. (Accessed: 22nd January 2019)