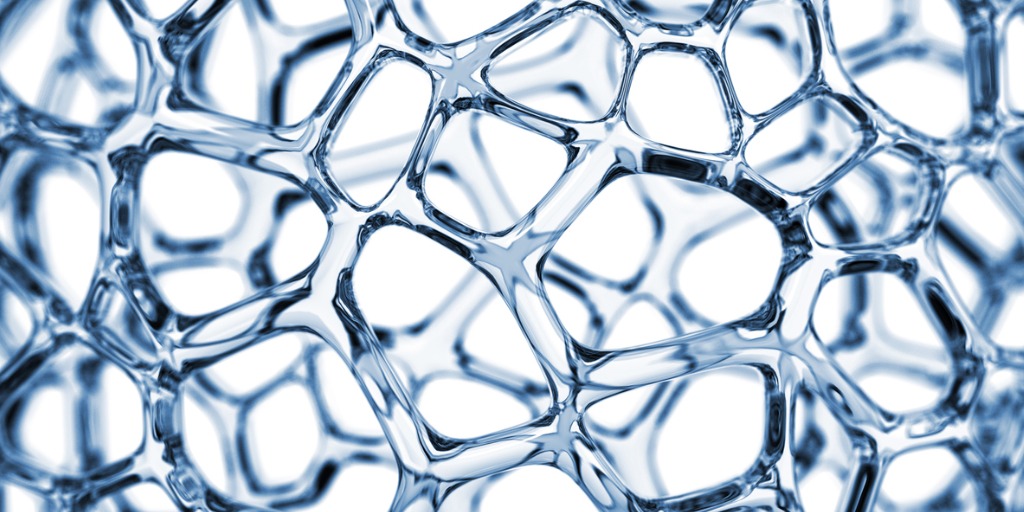
Sol-gel processes can be used to produce various high-performance solids including glasses and ceramics. In the world of glass production, sol-gel techniques offer a low-temperature alternative to traditional melt-quenching and thus save energy. These techniques can be used to produce an ever-growing group of materials with incredibly broad applications. Glasses produced via sol-gel routes can be highly pure and exhibit a range of other useful properties.
In this article, we take a look at how the sol-gel process was developed, how it works, and the properties of glasses produced in this way.
What is the Sol-Gel Process?
The sol-gel process is a manufacturing method in which bulk solid materials are produced from a solution of small particles. The process begins with the preparation of a solution of inorganic monomers, such as metal alkoxides and acetylacetonates; a hydrolysis agent, e.g. water; a solvent, e.g. alcohol; and an acid or base catalyst.1 The dissolved monomers undergo hydrolysis and polycondensation reactions to form a sol: a colloidal suspension of polymers or fine particles.
Further reactions form cross-links between the particles, solidifying them into a wet gel, which still contains water and solvents. Removing the water and solvents leaves a dry gel, one of the final possible products of the process. Further drying and heat treatment removes residual liquid and induces further polycondensation reactions, which can ultimately produce densified ceramics or glasses with novel properties.
Development of Sol-Gel Techniques
Sol-gel processes were first developed in the 1960s, with the purpose of producing bulk glasses at low temperatures, below 1000 C.2,3 These techniques contrasted greatly with conventional energy-intensive melting methods, which generally involve temperatures over 1400 C in furnaces.4 Years later, the rising popularity of optical fibers stimulated research into the production of silica glass preforms, from which optical glass fibers are drawn, via the sol-gel method.5
Producing silicate glass in bulk, e.g. rods and plates with dimensions exceeding tens of millimeters, was initially difficult due to the formation of cracks during the drying process. However, by the late 1990s, bulk silicate glass could be reliably and efficiently produced via a number of sol-gel routes. Alongside this research, efforts to produce more exotic multicomponent glasses, such as silicon oxycarbide glass, via sol-gel routes were proving successful, and enabling new glass compositions that could not be achieved with melt-quenching.6
Today, a huge range of multicomponent glasses and glass ceramics can be produced using sol-gel techniques, as well as more conventional silicate glasses.
Advantages and Properties of Sol-Gel Glasses
For similar chemical compositions, the overall structure and properties of sol-gel glasses are similar to those of conventional melt-formed glasses.4 Because of the high costs of specialized processing and raw materials for sol-gel approaches, they are not widely used for commercial production of ordinary silicate glass panels or containers. Instead, sol-gel techniques enable the production of specialized glass products which can’t be made using conventional techniques.
Low process temperature is one of the defining characteristics of the sol-gel approach, yet it is capable of producing a vast range of high-performance materials. When it comes to glass production, advantages over conventional melting include better homogeneity, better purity, and less energy-intensive production, although cost can still remain high. Critically, sol-gel techniques enable the creation of new materials with properties outside the range of conventionally made glass. These include useful electronic, optical, biomedical, mechanical and thermal properties that lend sol-gel glasses to a huge range of applications.
Applications of Sol-Gel Glasses
Some of the main applications of these materials are electronics, optics, thermal insulation, catalysis, and various mechanical and biological functions.
Electronics
Electronic components that can be produced using sol-gel glasses include capacitors and piezoelectric transducers.7,8 Novel applications of sol-gel glasses in this field include lithium-ion batteries and electrolytic membranes in fuel cells.
Optics
Sol-gel glasses can exhibit a range of useful optical and photonic properties. Often the sol-gel approach is used to deposit a glassy material in a thin film, where it has applications from colored coatings for car windows to laser elements, optical sensors and photovoltaics.9
Chemistry
Sol-gel techniques can produce materials with highly porous structures and very large internal surface areas. This lends them well to applications in catalysis, where the porous surfaces act as catalyst or catalyst-carrier. Such materials and applications include porous silica for chromatographic separation, and silicate-based catalysts for the production of H2. 10,11
Biosciences
Due to the high surface area and the easily controlled size and distribution of pores in sol-gel glasses, it’s possible to trap biological molecules or living tissues in porous glasses using sol-gel techniques. These high purity and homogeneous materials can be used for biomedical research and have been applied to the development of biosensors and tissue engineering techniques.12
The breadth of achievable properties of sol-gel glasses means that the range of possible applications for this class of materials is rapidly growing. As research continues, sol-gel glasses are redefining the way that we think about glass.
References and Further Reading
- Sakka, S. Handbook of sol-gel science and technology : processing, characterization, and applications. (Kluwer Academic Publishers, 2005).
- ROY, R. Gel Route to Homogeneous Glass Preparation. J. Am. Ceram. Soc. 52, 344–344 (1969).
- Dislich, H. New Routes to Multicomponent Oxide Glasses. Angew. Chemie Int. Ed. English 10, 363–370 (1971).
- Mackenzie, J. D. Glasses from melts and glasses from gels, a comparison. J. Non. Cryst. Solids 48, 1–10 (1982).
- Sakka, S. Fibers from gels and their applications. in Glass Integrated Optics and Optical Fiber Devices: A Critical Review 10275, 1027507 (SPIE, 1994).
- Pantano, C. G., Singh, A. K. & Zhang, H. Silicon oxycarbide glasses. J. Sol-Gel Sci. Technol. 14, 7–25 (1999).
- Hatono, H., Ito, T. & Matsumura, A. Application of BaTiO3 film deposited by aerosol deposition to decoupling capacitor. Japanese J. Appl. Physics, Part 1 Regul. Pap. Short Notes Rev. Pap. 46, 6915–6919 (2007).
- Tsurumi, T., Ozawa, S. & Wada, S. Preparation of PZT thick films by an interfacial polymerization method. in Journal of Sol-Gel Science and Technology 26, 1037–1040 (Springer, 2003).
- Yoneda, T., Yasuhiro, S. & Morimoto, T. Sol–Gel Coatings Applied to Automotive Windows. in Handbook of Sol-Gel Science and Technology 1–15 (Springer International Publishing, 2016). doi:10.1007/978-3-319-19454-7_84-1
- Lubda, D., Cabrera, K., Nakanishi, K. & Minakuchi, H. SOL-GEL PRODUCTS NEWS Monolithic HPLC Silica Columns. Journal of Sol-Gel Science and Technology 23, (2002).
- Gronchi, P., Kaddouri, A., Centola, P. & Del Rosso, R. Synthesis of nickel supported catalysts for hydrogen production by sol-gel method. in Journal of Sol-Gel Science and Technology 26, 843–846 (Springer, 2003).
- Baino, F., Fiume, E., Miola, M. & Verné, E. Bioactive sol-gel glasses: Processing, properties, and applications. Int. J. Appl. Ceram. Technol. 15, 841–860 (2018).